Right here is iVT’s full, in-depth case research of the most important mix harvester on the planet – New Holland’s CR11 – together with an in depth take a look at the all-new expertise
New Holland first launched its model new, fully redeveloped CR11 mix harvester to the general public finally November’s Agritechnica, within the course of touchdown a Gold Award for Innovation. It’s important promoting level to prospects was that being boosted with leading edge expertise, the machine can harvest crops with better effectivity and productiveness, whereas lowering grain loss and harvesting prices. It additionally occurs to be considered the world’s largest mix.
Taking the legacy of the corporate’s flagship CR line – notably topped by the CR10.90, world report holder for probably the most wheat harvested in eight hours – the brand new CR11 was designed, and is being produced, at New Holland’s Centre of Harvesting Excellence in Zedelgem, Belgium.
Highest productiveness in the marketplace
Subsequent yr marks the fiftieth anniversary of the New Holland Twin Rotor expertise, and the brand new CR11 highlights the benefit of the Twin Rotor idea that revolutionised mix harvesting. It’s due to the Twin Rotor expertise that the brand new CR can supply the very best productiveness at lowest grain crackage in the marketplace.
“The CR11 is a totally new mix constructed utilizing over 8,000 newly developed elements, which equates to over 90% of the elements used,” says Geert Nerinckx, New Holland’s CR11 international product supervisor. “It is a greater mix and is rather more productive than many in the marketplace. Its important objective is to scale back the full value of harvest for our prospects.”
Trying intently on the machine, and beginning with productiveness, the feeder channel has been made wider to permit extra materials via. It has greater rotors which might be 50% longer, and this permits the machine to feed straight into the resident system.
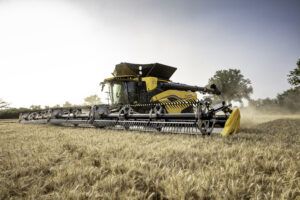
Improved backside line
Extra productiveness, near zero grain losses, higher and extra environment friendly residue administration and a big discount in downtime are the 4 pillars the CR11 was constructed on – and with the next total goal to scale back the full value of harvesting to enhance the farmer’s backside line profitability.
The CR11 is powered by an even bigger engine, the Cursor six-cylinder, 16 litre 775hp C16 engine by FPT Industrial. The mix’s grain tank capability has additionally been elevated
to twenty,000 litres.
“The grain obtain charge has been elevated to 210 litres per second which implies the larger grain tank will be emptied in lower than 100 seconds,” says Nerinckx.
Trade first
With a design objective of zero loss, the New Holland engineers developed the double cleansing shoe. The brand new Twin Clear cleansing shoe comes with two cleansing programs behind one another, with two higher sieves, two decrease sieves, two clear grain augers and two units of strain sensors to measure cleansing shoe load.
As an trade first, the brand new Twin Clear system is totally automated to ensure even cross distribution of the cleansing shoe, for max capability, however nonetheless with grain loss ranges near zero.
“When you have got such excessive capability of grain, it must be cleaned effectively, whereas ensuring there is no such thing as a grain loss,” says Nerinckx. “We gave our engineers the duty of designing a cleansing shoe with zero grain loss and so they got here very near that objective.
“We name it Twin Clear, which implies it has two cleansing programs in a single cleansing shoe. There’s a wider and longer cleansing pan which is adopted by two cleansing programs, and is all totally automated. It’s all a part of the IntelliSense info system of the mix, and repeatedly measures cleansing shoe load, left, proper and after, utilizing sensors. If it detects any anomalies left or proper, it’s going to appropriate the distribution robotically.”
Assembly future calls for
New Holland says it has designed the brand new CR11 in anticipation of the way in which during which future harvesting calls for will proceed to evolve. It additionally factored in suggestions from prospects looking for better capability, decrease grain losses and most safety of the grain high quality.
Recognising how greater yielding crops and unpredictable climate can have an effect on each one season’s crop and the subsequent, New Holland engineers aimed to design a machine that may play
its full half in delivering most productiveness, and clear fields rapidly to make sure high quality is protected and the next yr’s crop institution can happen in good time and in good circumstances.
“We’re working with 15m headers however have additionally examined 18m headers in Australia,” says Nerinckx. “Some contractors will want to unfold the residue materials over the total width of chopping, subsequently we’ve got a totally new automated resident system to do this.”
The CR11 comes with Intellispread and two radars, one on the left and one on the appropriate of the mix. Radar beams present the operator precisely the place the straw particles are touchdown within the area, even via the mud clouds generated by the machine.”
“Its important objective is to scale back the full value of harvest for our prospects”
Chop and unfold
The fully new residue administration system includes a brand-new chopper and chaff spreader system, designed to make sure the most effective chop high quality and even residue spreading over as much as 60ft chopping width.
The Intellispread radar system, winner of a 2022 Agritechnica Innovation Silver Medal, automates the spreading management to make sure full and even residue protection behind the mix, no matter wind results, crop sort or moisture circumstances.
“On the driveline, your entire cropflow channel is wider, however the transport width remains to be the identical,” says Nerinckx. “We had been in a position to obtain that by placing a few of the drives contained in the channel. For instance, we’re utilizing the left rotor for the driveshaft of the Dynamic Feed Roll. That’s implies that your entire DFR driveline goes away and you’ll widen the cropflow channel since you are driving the DFR together with your rotor.”
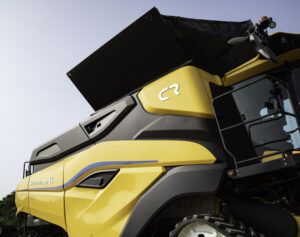
Lowered downtime
The engineers additionally got here up with a brand new automated unblocking process, designed to scale back machine downtime. Whereas the brand new CR11 mix is able to be pushed for max throughput, New Holland recognises that it’s inconceivable to fully get rid of any threat of plugging the machine with straw. Within the unlikely occasion of operator error inflicting a blockage within the mix, the automated system to unblock will kick in and information the operator via an unplugging process in a approach that clears the mix in minutes somewhat than hours, with out requiring the operator to exit the cab or carry out any bodily effort.
No concern of blocking
As a result of it considerably reduces downtime attributable to such a state of affairs, the automated reverser helps and encourages the operator to take advantage of the mix’s full capability potential with out concern of blocking. As well as, this characteristic will increase security whereas clearing a blockage, as a result of no particular person is leaving the cab in the course of the automated unplugging course of.
Fewer drive parts
Downtime prevention is additional aided by the mix’s revised driveline simplicity with as a lot as 25% fewer drive parts and with the elimination of all chain drives.
“One other good thing about this mix is that we not have any drive chains, solely belts, shafts and CVT drives,” says Nerinckx. “With 25% fewer drives, the profit is the operator can unblock the mix from contained in the cab.
“Each mix driver who has blocked the machine and is aware of it might probably take hours to clear it out. With this method, if a blockage happens, the mix itself will seek for the blocked materials, clear the blockage, pull the fabric via, and inside 5 to 10 minutes regular harvest operations can proceed once more, with the operator by no means leaving the cab.”
Greatest seat in the home
Contained in the cab of the CR11, New Holland has mounted the brand new Intelliview 12 show and IntelliSteer steerage system, along with different important precision farming features resembling telematics and distant display screen viewing, for ease of use.
Additionally, NutriSense comes with a NIR sensor that displays crop high quality by way of using close to infra-red gentle to analyse vitamins like protein, starch and oil contents, plus moisture ranges, and might create maps of those for additional agronomic evaluation.
“The cab additionally comes with a bunch of upgrades,” says Nerinckx. “It has a putting new design, new seat and a model new console. A brand new console was crucial as we’ve got 10 new controls, that had been handbook outdoors the cab, and are actually contained in the cab as distant controls. Distant controls provides consolation to the operator and in addition reduces the downtime of the machine, as there is no such thing as a have to cease and go outdoors to alter the handbook controls. These distant controls within the cab will be automated.”
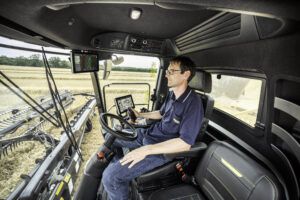
The proper monitor
Seen upgrades on the brand new CR11 mix embrace the brand new 15m (50ft) draper header manufactured by MacDon for New Holland.
Recognising the developments for decreased floor compaction together with transport width laws, the CR11 presents a variety of wider tracks and larger tyres.
The machine at Agritechnica was fitted with tyres from Michelin, the Michelin Cerexbib 2, measurement 900/65R46 with a diameter of two.32m, that are the results of a co-development between New Holland and Michelin.
Subsequent-level tyre measurement
New Holland says that is the primary time that this subsequent degree of tyre measurement has been launched on a mix of any sort, and the longer tyre footprint and elevated traction present a decreased floor compaction with no precedents in harvesting.
Visually, the producer believes that shut collaboration between industrial design and engineering groups, along with product specialists and model advertising, created such a brand new, impressionable design that focuses on buyer wants in addition to aesthetic sensibilities.
The tip result’s an iconic, refreshed design that’s trendy but timeless. The circulate of the harvest is underlined on the outside panels by the dynamic blue characteristic that runs throughout the modern physique via the varied features.
This text additionally seems within the June/July 2024 version of iVT Worldwide