In an business shifting at tempo, thermal administration, cushioning, and sealing applied sciences are redefining how battery packs are designed, assembled, and guarded.
Responding to the elevated complexity in battery pack design because of the evolution of EVs and hybrids, science-based innovator, 3M, designs and manufactures barrier supplies, cushioning supplies, and sealants.
With a portfolio that features thermal runaway obstacles, cushioning foams, sealants, and extra, the worldwide firm is addressing crucial points reminiscent of thermal administration, battery pack meeting, value discount, and manufacturing effectivity.
One of the crucial urgent issues in Li-ion battery methods is thermal runaway. To assist tackle this design problem, the corporate presents its 3M Thermal Runaway Barrier 600/700 Collection, which comprise a compressible, flame-resistant, thermal insulation mat materials. Able to withstanding temperatures as much as 1,200°C, these keep structural integrity even in excessive environments.
Anja Rohmann is a complicated software engineering specialist. She says, “The mat options non-classified fibers, has good flame resistance, and is designed to assist decelerate warmth switch from one cell to the subsequent. And each sequence might be utilized between cells to assist cut back thermal transport in excessive temperatures.”
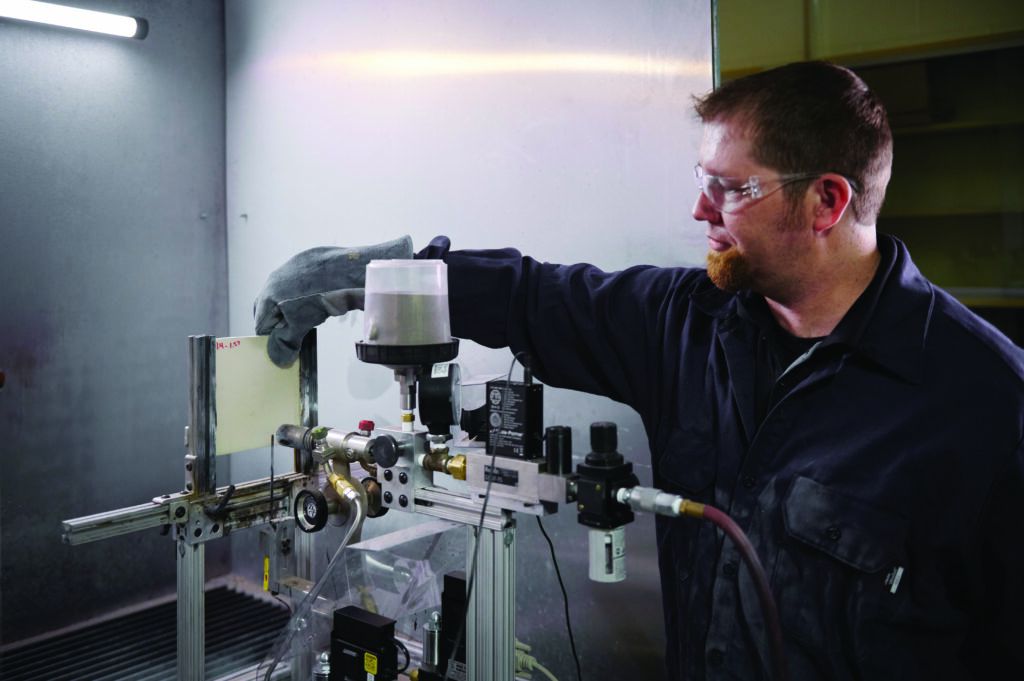
Rohmann explains {that a} key problem in battery pack meeting is sustaining constant strain inside the battery whereas absorbing mechanical stresses and vibrations. 3M Cell Growth Foam SJCEF is a flame-retardant microcellular polyurethane foam that meets this want. Its self-tacky properties cut back course of steps and meeting time, serving to to streamline operations. Rohmann provides, “It options customizable compression plateau for constant battery strain and is available in a variety of thicknesses, which suggests the fabric can accommodate a number of battery designs with out compromising efficiency,” making it ultimate for each EV and hybrid functions.
Battery enclosures should be sealed to stop moisture ingress, defend inside elements, and allow future serviceability. 3M Sealant SZ1000 for EV Enclosure Sealing is a two-part, cure-in-place foam sealant designed to fulfill these buyer wants. Providing flame retardancy, wonderful getting older sturdiness, and automatic dishing out compatibility, it helps producers to fulfill strict enclosure specs whereas sustaining manufacturing throughput. Rohmann explains that whether or not utilized in EVs or hybrids, the sealant performs a crucial function in sustaining long-term battery pack integrity in various environmental circumstances.
In keeping with Rohmann, product growth within the battery sector is something however static. Certainly, OEMs are regularly refining their designs to fulfill shifting efficiency, value, and security targets. She feedback, “The client develops and optimizes their battery designs very dynamically in response to continuously altering challenges from the business. This may generally be very short-term. Our expertise is essential in anticipating sure materials properties or incorporating them prematurely.” This fast iteration cycle presents a problem for materials suppliers, however 3M is ready to stay agile with out sacrificing high quality or reliability.
3M’s method to innovation hinges on direct engineer-to-engineer collaboration; that is what the corporate refers to as ‘bench-to-bench’ growth, upon which Rohmann expands: “Shut collaboration with the OEM is essential for the success of growth. As soon as key alternatives are recognized, having engineers sit down and discuss by way of technical challenges allows everybody to know the place the ache factors are. Typically these are within the product idea, generally in learn how to combine an progressive thought into the manufacturing course of. By way of shut collaboration, each events have the chance to study in regards to the feasibility, growth potential, and limitations of one another.”

Certainly, it’s right here when an OEM’s challenges turn out to be 3M’s challenges. “A main concern of OEMs is value discount,” she says, including, “Lowering the price of battery packs to make electrical automobiles and different functions extra inexpensive is a serious problem.” This, she reveals, entails optimizing manufacturing processes and materials utilization, as effectively balancing efficiency with materials and manufacturing prices.
After which there are challenges related to thermal administration. As vitality density will increase, so does the problem of larger warmth launch. “Effectively managing the warmth generated to handle security and efficiency is crucial,” she displays, declaring that superior supplies with excessive thermal stability and low conductivity are presently being developed by 3M to handle this.
Whereas early battery pack designs centered on single-purpose supplies, over time the business has shifted to multi-purpose supplies, as Rohmann explains, “With larger give attention to automobile affordability and industrialization, OEMs are in search of options that not solely meet the applying targets, however achieve this in a means that may be simply built-in into their manufacturing processes.” She reveals that OEMs are additionally in search of materials options that assist tackle a number of necessities distinctive to the brand new chemistry and type elements which are available on the market.
“Within the case of thermal runaway obstacles, which means the necessities for the chosen supplies nonetheless want to stay extraordinarily excessive by way of thermal stability, however they have to now additionally provide wonderful elasticity and prolonged sturdiness.” This nuanced stability of properties requires a deep understanding of supplies science and steady suggestions from real-world functions, one thing which 3M is uniquely positioned to perform.
It’s simple that security and environmental laws are additionally shaping product growth, as Rohmann feedback, “Laws for EVs and thermal occasions are designed to assist tackle security, efficiency, and environmental compliance.”
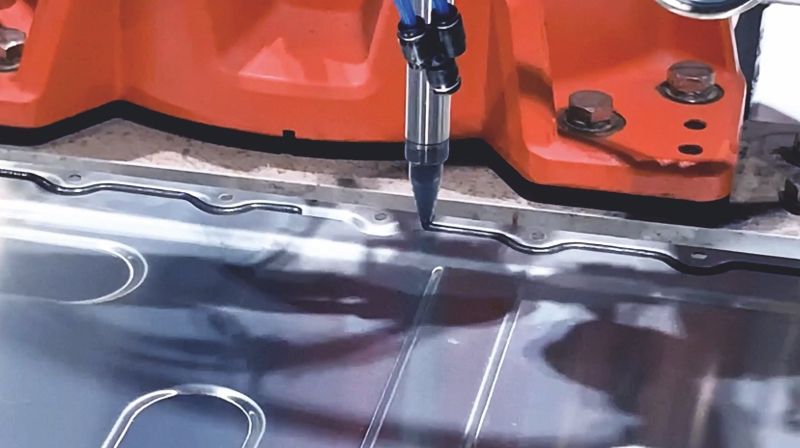
Right here, environmental mandates, such because the EU Battery Directive and Finish-of-Life Car Directive, are influencing designs by encouraging using supplies that may assist with disassembly and recycling. These elements are integrated into the corporate’s R&D plans to take care of future-ready options.
Whereas EV and hybrid battery packs face totally different challenges, reminiscent of vitality density for EVs and ICE integration for hybrids, many options might be shared or complementary between platforms. Advances in battery know-how, thermal administration, and management methods for one kind can usually be tailored for the opposite,” says Rohmann “and enhancements in manufacturing effectivity and price discount strategies can profit each full EVs and hybrids.”
This cross-pollination of concepts and applied sciences is what’s going to allow strong, versatile options which are able to addressing the complete spectrum of EV necessities. “By addressing these challenges with progressive options and leveraging synergies between full EV and hybrid applied sciences, we are able to improve the efficiency and competitiveness of each varieties of automobiles,” Rohmann concludes.